Product Knowledge---Solution to the Cracking of Vibrating Screen’s lateral plate
Date:2019-04-12
In the current crushing industry, vibrating screen is a widely used screening equipment, which has advanced structure, strong exciting force, low vibration noise, easy maintenance, strong durability and so on. It is widely used for classification in mining, mineral processing, coal preparation, building materials, chemical industry and other industries. As an important equipment in the industry, the performance of vibrating screen directly affects the production capacity and technical and economic indicators. Therefore, it is necessary to master some common fault diagnosis and solutions of vibrating screen in production practice.
Vanguard Machinery has collected the feedback information of customers who are using vibrating screens in recent years, and proposed a treatment plan for the cracking of lateral plate during use.
Difficulties in Treatment of the Lateral Plate’s Cracking
Vanguard Machinery has collected the feedback information of customers who are using vibrating screens in recent years, and proposed a treatment plan for the cracking of lateral plate during use.
After a long period of operation, the vibrating screen is prone to fracture of crossbeam and track beam and crack of side plate. Fracture can be solved by replacing the crossbeam and track beam. As for the crack of side plate, it will appear again soon if welding treatment is adopted, because welding stress can not be eliminated.
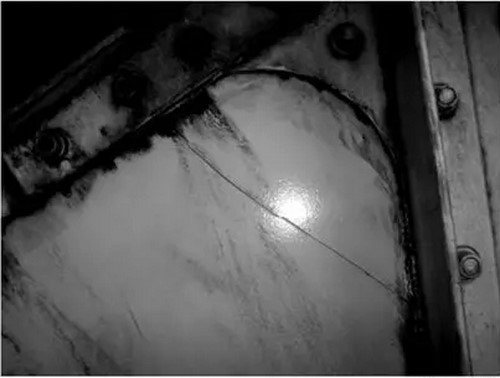
Fig.1:Cracked side plate
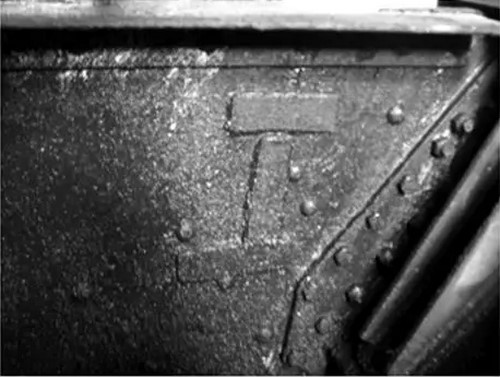
Fig. 2: Plate-adding welding
The frame structure of vibrating screen is riveted together by riveting bolts. If we want to replace the cracked side plate(as shown in Fig. 1), first of all, hundreds of riveting bolts on the side plate should be removed, and it’s a heavy workload which is tantamount to reassembling a sieve. There is neither site nor time for such treatment. If a simple welding process is carried out, including plate-adding welding (as shown in Fig. 2), it does not work well under the vibration condition, instead aggravate the extension of cracks or other new cracks, because the welding stress of the side plate can not be eliminated.
Specific Treatment Methods
(1)Firstly, check the reliability of hexagonal bolt connection in crack area. Remove the riveting bolts on angel steel of the side plate and the upper reinforcing plate to check the damage between the angle steel and the mating surface of the plate. When the surface is qualified, ensure the alignment of both ends of the side plate’s crack(as shown in Fig. 3).

Fig. 3: the alignment of both ends of the side plate’s crack
(2)(2)2.Grinding a groove (inside of the sieve) along the crack center over the entire length. (as shown in Fig. 4)

Fig. 4: Grinding a groove
(3)Weld vertically along the direction of the crack and the sieve plate (welding torch can not swing; weld in two sections), and strike with the needle gun after each weld to eliminate the stress and welding slag, as shown in Fig. 5

Fig. 5 Vertical welding along the direction of the crack and the sieve plate
(4)4. Carry out continuous vertical welding, and each weld is hit with a needle gun until the welding is completed, as shown in Fig. 6

Fig. 6 Continuous vertical welding
(5)Grind and polish the weld seam until the surface is smooth and even with the side plate surface, as shown in Fig. 7.

Fig. 7 Grind and polish the weld seam
(6)6. Grind the weld on the outside of the sieve, and minimize direct grinding of weld. Just clean the weld and expose the base material, then weld it like the inside.See Fig. 8 and 9, respectively.

Fig. 8 Outside grinding

Fig. 9 Outside welding
(7)Grind the outer side of the side plate.
(8)Grind and shape the holes in the top of the side plate (holes in the weld) to ensure that all burrs have been removed without grooves and dents, as shown in Fig. 10
Fig. 10 Grind and shape the holes in the top of the side plate
(9) Polish the coating in the finishing area and apply a primer (both on both sides) to the side plate and the reinforcing plate. Place the reinforcing plate on the inside of the sieve and install as many bolts as possible. The reinforcing plate covers both sides of the weld repair area, as shown in Figure 11. The dotted line in the figure is the reinforcing plate.
(10)After tightening the bolt, drill a number of holes in the reinforcing plate to ensure that cracks are covered, and install riveting bolts in the holes to tighten, as shown in Fig. 12.
(11) Grind the repair area at the top of the side plate, the angle steel and the inside of the side plate, and coat with primer. Add a reinforcing plate to the inner corner steel and rivet with at least three riveting bolts on both sides of the weld seam, as shown in Fig. 13.
Fig. 13 add a reinforcing plate to the inner corner steel
(12) When all riveting bolts are riveted, paint the repair area. And seal the reinforcing plate with SIKA adhesive to prevent corrosion after the topcoat is dried.
Replacement or tension should be carried out when necessary; check the final running speed; prepare two groups of cards to test no-load and load.
This method is simple and easy to handle, saving time. The vibrating screen repaired by this method has no cracks, which proves the feasibility and reliability of this maintenance scheme.
Vanguard Machinery has collected the feedback information of customers who are using vibrating screens in recent years, and proposed a treatment plan for the cracking of lateral plate during use.
Difficulties in Treatment of the Lateral Plate’s Cracking
Vanguard Machinery has collected the feedback information of customers who are using vibrating screens in recent years, and proposed a treatment plan for the cracking of lateral plate during use.
After a long period of operation, the vibrating screen is prone to fracture of crossbeam and track beam and crack of side plate. Fracture can be solved by replacing the crossbeam and track beam. As for the crack of side plate, it will appear again soon if welding treatment is adopted, because welding stress can not be eliminated.
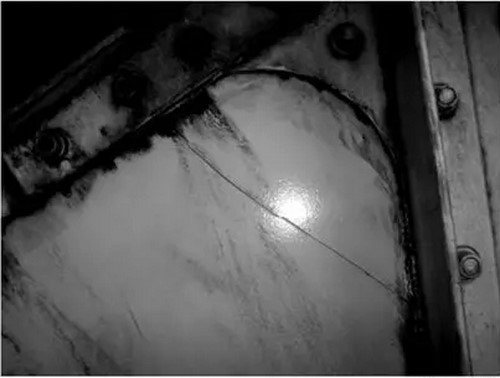
Fig.1:Cracked side plate
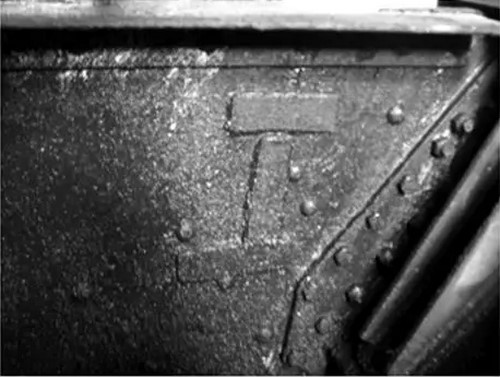
Fig. 2: Plate-adding welding
Specific Treatment Methods
(1)Firstly, check the reliability of hexagonal bolt connection in crack area. Remove the riveting bolts on angel steel of the side plate and the upper reinforcing plate to check the damage between the angle steel and the mating surface of the plate. When the surface is qualified, ensure the alignment of both ends of the side plate’s crack(as shown in Fig. 3).

Fig. 3: the alignment of both ends of the side plate’s crack

Fig. 4: Grinding a groove

Fig. 5 Vertical welding along the direction of the crack and the sieve plate

Fig. 6 Continuous vertical welding

Fig. 7 Grind and polish the weld seam

Fig. 8 Outside grinding

Fig. 9 Outside welding
(8)Grind and shape the holes in the top of the side plate (holes in the weld) to ensure that all burrs have been removed without grooves and dents, as shown in Fig. 10
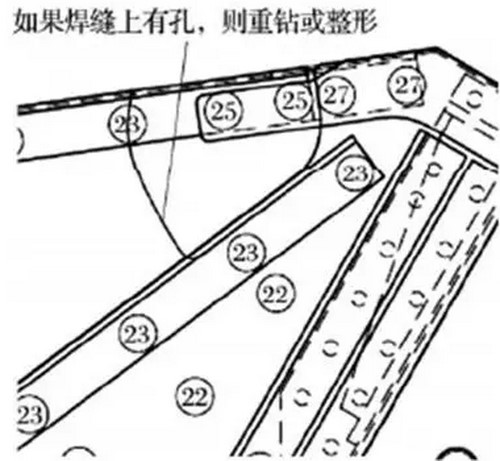
(9) Polish the coating in the finishing area and apply a primer (both on both sides) to the side plate and the reinforcing plate. Place the reinforcing plate on the inside of the sieve and install as many bolts as possible. The reinforcing plate covers both sides of the weld repair area, as shown in Figure 11. The dotted line in the figure is the reinforcing plate.
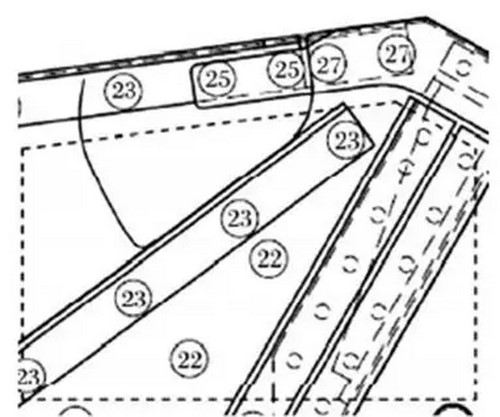
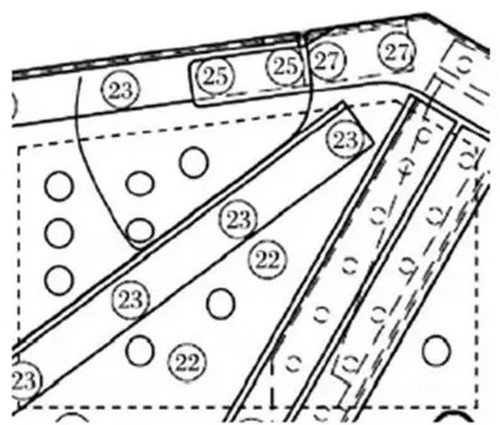
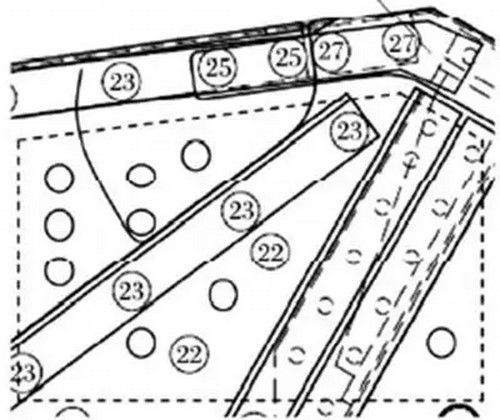
(12) When all riveting bolts are riveted, paint the repair area. And seal the reinforcing plate with SIKA adhesive to prevent corrosion after the topcoat is dried.
Replacement or tension should be carried out when necessary; check the final running speed; prepare two groups of cards to test no-load and load.
This method is simple and easy to handle, saving time. The vibrating screen repaired by this method has no cracks, which proves the feasibility and reliability of this maintenance scheme.